Composites
for your DARKSIDE VW...
I wrote a two (2) part article for the
DDSG newsletter about composites. These articles get into the basics of
composites materials and fabrication. Part One is
the materials and Part Two is the fabrication. Just
click on the book cover below to read the article of your choice.
For those of you waiting anxiously for
Part Two......it is still not done. However, I was looking through my archives
and came up with some e-mails that I wrote that concern composite fabrication.
I have added them to my webpage here. Just follow the links below for the
information of your choice. Many of the links go to the same place, so
don't be surprised when you don't see something new with each one.
Mold Making - Tonneau
Cover
Mold Making - Fenders
Part Lay-up
Floorpans
Composites
101 - Part One
Introduction
Why do you want composites on your DARKSIDE
VW? Composites have several advantages for the custom VW owner. They do
not rust or corrode, making them ideal for replacement of rusted-out body
panels. They are lightweight, typically saving 25% over the steel parts
they replace. Lighter car translates to better performance and fuel economy.
Composites are also able to be formed into shapes that can not be formed
in steel and can be fabricated very inexpensively making body mods a reality
for the DARKSIDER. I will cover fabrication in detail next time.
What is a composite?
Well, composites are a class of materials that use two or more different
materials in combination. This combination of materials has better properties
than the sum of the individual properties. There is a synergy between the
materials. The most common automotive composites are glass fiber reinforced
plastics. Fiberglass is the common name, but
a bit of a misnomer. The fiber glass is actually only one of the materials
that make up the composite. It is the reinforcement. The matrix of the
composite is typically a thermoset plastic resin (polyester is the most
common). I will discuss materials in more detail later.
Why should you listen to me? Well, actually
you are reading this and you could stop anytime. But, if you got this far
you are probably considering composites for your T3 and just so you know
I have not been breathing too much resin fumes, I have a Master's degree
in structural composite design and spent 15 years designing with and for
composites. The last 9 years with Ford Motor Company doing research in
advanced materials (composites) for body structures. Enough about me....on
with the show.
Part One Materials (string and glue)
This is the starting point. I will try
not to get too technical, but will provided some good basic information.
Composites are often jokingly referred to as string
and glue. It is not a bad description. Most automotive composites
are basically two components: the reinforcing fiber (string) and the plastic
matrix or resin (glue). The fiber provides the bulk of the strength of
a composite and the matrix holds it all together, gives it shape and stability,
and adds toughness be distributing the stresses among the fibers.
Let's talk about the String first.....
The string for automotive composites is
almost exclusively glass fiber. Glass fiber comes in two basic grades:
e-glass or electrical grade and s-glass or structural grade. The auto industry
uses e-glass exclusively and we should too. It is much cheaper than s-glass
which was developed for the aerospace industry and e-glass is more than
adequate for anything you would do for your DARKSIDE ride.
E-glass fiber is available in many forms.
The most common ones and some comments are listed below.
Tow - This is simply a
spool of glass fiber. A tow is made up of about a 1000 individual glass
strands twisted into a thread. This form is not particularly useful to
the DARKSIDER.
Chopped Mat - The mat consists of
randomly oriented short glass fibers (1-2 inches long) held together with
a small (2-4%) amount of thermoplastic binder. The binder simply holds
the short glass fibers together until the part is molded. CSM Continuous
Strand Mat (CSM) is a random oriented mat made of swirls of continuous
glass fiber. It is also held together with a small amount of binder until
molded. CSM is the most common form of reinforcement used in the auto industry.
Woven - Woven fabrics are clothes
of fiberglass tows. They have a bi-directional orientation to the tows.
There are many different weaves available from plain weaves to satins to
twills. Not used commonly in the auto industry due to the cost of the fabrics.
Those are the basic fiber forms for automotive
use. There are lots more when you start looking at the aerospace industry.
Everything from uni-directional tapes to stitched fabrics to 2-D and 3-D
braids. The auto industry has prototyped some of these advance fiber forms,
but the cost is always too high.
The other reinforcement you may be interested
in is carbon or graphite fiber. These fibers are significantly (3 times)
stiffer than glass fiber and are common in everything from skis to golf
clubs to jet fighter aircraft. You don't find them in cars very often unless
you look at F1 or Indy cars. The reason you donÕt see them - COST.
Carbon is at best $8 per pound and can be as much as 100 times that for
the highest performance versions. Compare that with glass at about $1 per
pound and it is easy to see why it is not used on your Escort, Accord,
or New Beetle. If you do see it, such as on the Momo steering wheel or
the shift knobs, it is almost always a photographic reproduction, not real
carbon fiber. I donÕt think the DARKSIDER has to worry about carbon
for strength. If you have money to burn and want the look of carbon fiber
or want a super light and stiff part, then take a look at carbon, otherwise
stick to glass.
Now for the Glue.....
There are two basic types of glue (matrix)
used in automotive composites: thermoset and thermoplastic. Thermosets
are resins that are most commonly two liquid components that when mixed
together in the proper ratio cure into a solid plastic. Once cured, thermosets
can not be reformed. Thermosets are going to be the matrix of choice for
the DARKSIDER. More in a minute on thermosets.
Thermoplastics are resins that start out
as a solid, are melted into a liquid for fabrication, and allowed to cool
to harden up again. Thermoplastics can be reformed by heating them up and
reshaping them and then allowing them to cool again. Thermoplastics are
not practical for the DARKSIDER to use. The molding temperatures are high
(like 300-800F), the materials more expensive, and they offer little or
no benefit over thermosets from a structural point. The auto industry is
interested in them primarily because they are easier to recycle.
For the DARKSIDER, there are two thermoset
resins to choose from: polyester and epoxy. There are lots of others available
and many different brands to choose from, but polyester resin and epoxies
are the two most common and readily available to the DARKSIDER. Polyester
resin is commonly used in the boating industry as well as the auto industry.
It is strong, lightweight, pretty tough, easy to work with, and most of
all CHEAP. Epoxy resins offer more strength and significantly higher temperature
resistance than polyesters, but are also much more expensive.
For almost all composites applications
on a DARKSIDE VW, polyester resin will be more than adequate when combined
with chopped mat or CSM glass reinforcement. I would only use epoxy resins
around the engine compartment or in areas that would be soaked in gasoline
or windshield washer fluid on a regular basis. Epoxies offer better chemical
resistance. As an example, I will probably use epoxy resin when I fabricate
my custom rear valance panel since it is very near the exhaust. Polyester
might be adequate if I were to provide some heat shielding on the backside
of the panel. Another example might be the custom intake plenum Jake Kooser
is planning for his 2.0L high performance engine, a high temperature application
with potential for gasoline exposure. For all other projects, fenders,
hoods, decklids, spoilers, ground effects, dashes, etc; polyester resin
is more the adequate.
Most thermoset resins come in two components:
a base polymer and a catalyst or hardener. The two are mixed together to
start the curing process. Once the curing reaction starts, you can't stop
it. It will harden. The time it takes to harden is called the pot life
or working time. This is usually after the material is about 50-70% cured.
The part will continue to cure for quite some time after that, some times
taking a month to reach 99% cured. Don't worry about waiting a month to
use your parts, 99% of the strength and stiffness of the composite is reached
at 80% of the cure which is usually reached inside of 24 hours.
DO worry about the pot life or working
life of the resin you choose. You have seen 5 minute Epoxy at the hobby
store......it has a 5 minute pot life. They make catalyst for both polyester
and epoxy that can give you very different pot lifes. Some catalyst will
cause the reaction to reach 80% cure in a couple of minutes (not good for
the DARKSIDER at home, but great for high volume molding of parts in the
auto industry), others will take hours or days to reach 80% cure. For the
DARKSIDER working at home look for a resin system (polymer and catalyst)
that gives you around hour of working time. This will leave plenty of time
for the fabrication methods I will discuss next time, but not leave you
waiting around for days for the part to be ready to install on your T3.
Well, that's Composite Materials 101. If
you made it this far without falling asleep....you pass. It also means
you are still interested in putting composites on your DARKSIDE ride, so
check out Part Two.
In Part Two I will
discuss in detail basic fabrication of composite parts, the fabrication
of molds for your composite parts, and how to attach your composite parts
to your VW.
Go to Part Two
Composites
101 - Part Two
////////////UNDER
CONSTRUCTION\\\\\\\\\\\\
Please check back later
Go to Part One
Composites
Resources
////////////UNDER
CONSTRUCTION\\\\\\\\\\\\
Please check back later
Fabricating
a Composite Tonneau Cover
It is in the
context of T1 Ghia, but you get the idea....
As for building the thing, assuming you
are only making one, here's what I would do.
I would start by removing the softtop.
Then, using masking tape, mask off the body where the cover will touch.
Pay close attention to masking off the bracket locations. Make a simple
steel plate (1/4" thick) that will let you drill and tap for the mounting
brackets. Thess steel brackets will get molded into the composite cover
and then be drilled and tapped after molding. I am not familiar with the
monting brackets on the K-G top so you will have to wing this one.
Once you have the mating surfaces masked
off and plenty of mold release applied, lay-up a 1/8 to 1/4 inch thick
layer of fiberglass and resin on the mating surface lettng it bo at least
an inch bigger then where the finished edge will be. Press the steel brackets
into the resin before it cures and then add an additional layer over the
top of the bracket. I would sandblast the bracket, degrease it and paint
it with good primer before inserting it.
Let this mating surface cure over night.
Once cured, pull it off of the body. This might be a good time to drill
the mounting holes in the brackets. Not sure. Now that you have the mating
surface done, put it back on the car. You are going to build up a rough
core of foam. Buy the blue insulating foam sheets at your local home building
supply outlet. Build it up by laminating together with 5 minute epoxy.
Once you have the core roughed in, shape
it using a rasp, grinder, sandpaper, or cheese grater. It should end up
just undersized since you will be laying the composite on top of it. Once
you are happy with the shape of the cover, began laminating it with fiberglass
cloth adn resin. Again try to get a 1/8 to 1/4 inch layer of composite.
At the edge of the mating surface, simpley laminate the outer skin to the
mating surface composite you created earlier. Remember the 1 inch or so
of extra that you left.
Because you are only making one, it does
not make sense to make a mold. Without a mold you will have to do a bunch
more hand finishing of the composite, but this will be no more than would
be necessary for the mold. Once the outer skin cures, trim off the edge
with the mating surface. Grind this down some and add a strip of fiberglass
and resin across the joint to strengthen it.
Now you just have to sand and fill the
surface until you are happy with it and then paint it. You can also go
underneath after it is all cured and grind away a bunch of the foam so
that it is maybe 1/2 to 1 inch thick. To really make the cover tough, add
a layer of fiberglass and resin to the underside after shaping the foam.
If you do this, you could probably stand on the cover.
This is how I would make the cover.
Fender
Mold Making
Most, if not all, aftermarket/specialty
fiberglass auto parts are molded in single sided molds. That is they make
a female mold from the original part and then spray chopped fiberglass
and resin into the mold to make the part. The mold is relatively inexpensive
and the composite materials are quite cheap. There is a good deal of labor
involved but not too bad.
The problem is that there is poor, at best,
control of the thickness of the part and the inside surface of the part
is not very good. The one part (floorpan) that I have from Fiber Innovations
is made this way and the thickness varies by more than 300%! You also don't
get the best strength form this process. You might only end up with 18-30%
glass fiber (the strong part of the composite) and the rest resin. Structural
composites typically start at 40% and go up to 65% fiber content. Low strength
composites are fine for fenders and such, but I would not wnat to rely
on them for structure(floorpans). For these parts you want better control
and more fiber...but that is another subject.
The other problem with this technique is
that you can not mold undercuts or return flanges. The part would be stuck
in the mold. To accomplish this you have to invest in much better and more
sophisticated molds that are two sided and multi-piece. Lots of $$$$.
I agree with Dave Hall...the vents on Square
and Fasty rear fenders would be a problem to mold in fiberglass. You really
need to design the part for the material and not just do a material substitution.
You could probably get a pretty decent vent, but it would require a bunch
of hand trimming and finishing.
Someone asked if an original fender would
be required. That would be the easiest way to get a good part, but you
would actually need the whole car. You would need to take the mold off
of the fender while it was bolted to the car to ensure that the fender
retained the correct shape. You would then have to add the flange details
to the mold after unbolting the fender. The molded fiberglass part can
not be "flexed" into the correct orientation like the steel part and the
steel fender is not rigid enough to guarantee that the fender would be
right unless it was bolted to the car.
Floorpan
Installation
PART ONE
The installation instructions that came
with my floorpan section from Innovations had you install the fiberglass
pan from the bottom of the car with self-tapping sheet metal screws and
then seal the whole thing up with silicon sealant. There are two main issues
with this installation procedure. The most important is the sheet metal
screws. This is NOT the way to join a composite panel to anything. Each
one of those screws will act as a starting point for cracks in the composite
and they will provide local stress risers...increasing local stress around
the screw by factors of 10 or more. Not good. The second issue is with
the installation from the bottom. Any weight that is put on the floorpan
will only be reacted by the screws. The floorpan is essentially hanging
from the screws.
So...how would I do it.
First I would install the floorpans from
inside the car. I would cut out the existing rusted steel floorpan trying
to leave a 1/2" or so flange around the perimeter. I would then careful
trim the composite floorpan to fit on top of this flange. I would then
drop the composite pan in from the top. It should be self support. Much
better from a stress standpoint. You are distibuting the load equally around
the perimeter rather than at each screw.
Now to attach the composite floorpan, I
would use an epoxy adhesive. It is more expensive than the sheet metal
screws, but it is structural and will be far more effective. You will need
to thoroughly clean the existing steel and I would apply a rust inhibiting
product like POR-15 at this point. You will also need to rough up the composite
where it will meet the steel. Just some 80 grit sanding...nothing to aggressive.
Then glue the floorpan in place with the epoxy adhesive. Run a bead of
epoxy all the way around the perimeter and then squeeze the floorpan down
into it. You could use a couple of screws to hold everything until it dries
(just pre-drill the composite), but then I would remove the screws and
seal the holes with some silicon. Once the epoxy dries, prime and paint
everything. Now go back and seal the edges with some silicon sealant to
keep water from getting into the seams and rusting out the sheet metal.
You will now have a floorpan that is an
integral part of the cars structure and will never rust out again. I think
Innovations floorpans will work OK for an application as I described above
assuming that the seat rails are intact and sound and that the seat is
not mounted to the composite. Just watch out for excessively thin spots
in the composite floorpan.
MORE ON FLOORPANS.....
I went and grabbed the section of Innovations
floorpan I have left in my basement and measured it. The thinnest section
was about .040 inches. The thickest section was 0.200 inches. That works
out to be 500% variation in thickness by my calculations. My original estimate
of 300% was a bit low. Granted this was the extreme of the thickness variation,
but even in the relative flat of the floorpan the thickness varied by more
than a factor of 2.
This does not surprise me since the floorpan
is obviously just sprayed up in an open mold by hand. This is the only
way to make these parts at this low volume and still make money. You will
always have this kind of variation with this manufacturing process.
Sorry, but I still think the floorpan quality
is medium at best.
And on the seat rail issue. I agree that
it would be difficult and ill advised to try to mold this part from composites.
For our T3's (at least the pre-72s) it is really a non issue since the
rails are not mounted to the floorpan, but to the tunnel and rocker. I
have seen seat mounting points and seatbelt mounting point successfully
molded into composite parts. These hardpoints can easily handle 35mph federal
front crash testing, but they are not simple through bolts.
AND EVEN MORE....
I have to agree with Scott Keck about the
stress riser problem around the screws that Innovations recommends installing
their floorpans with. This is a real problem and my biggest issue with
their installation procedure (there are couple of others), BUT there is
nothing wrong with having fiberglass underfoot. Unless you get a good sized
rock under your boot and somehow put all of your weight on the top of that
rock and you don't have carpet or anything covering the fiberglass, and
even then it will probably be fine.
I built and drove complete cars while at
Ford that had nothing but fiberglass composite body structures including
the floorpan. Typical thickness of the fiberglass composites for these
structures was only 2.5 - 4.0 mm (.100 - .160 inches). If the materials
are used properly they really can be stronger than steel. The 4x stronger
number that Innovations mentions is about right if you build the composite
part to be the same stiffness as the steel part. This is the usual design
approach for automotive composites. These materials are very tough and
the normal loads applied by moving around in your car and getting in and
out will not be a problem....if you install the floorpans right!
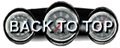
|